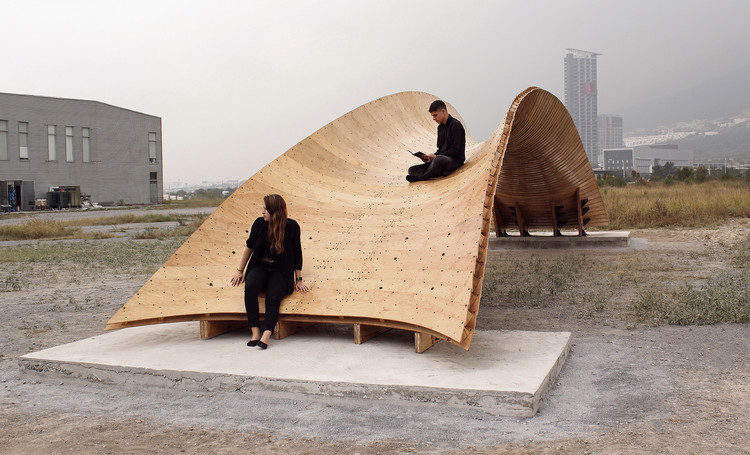
From its starting to point as a tree to its product form as a beam or piece of furniture, wood used in architecture and interior design goes through several stages and processes. A renewable resource and popular traditional building material, wood is also often cited as a promising construction material of the future, one that is suitable for the new demands of sustainability. But unlike concrete, whose molds can create even the most complex curves, wooden architecture most commonly uses straight beams and panels. In this article, we will cover some techniques that allow for the creation of curved pieces of wood at different scales, some of which are handmade and others of which seek to make the process more efficient and intelligent at a larger scale.
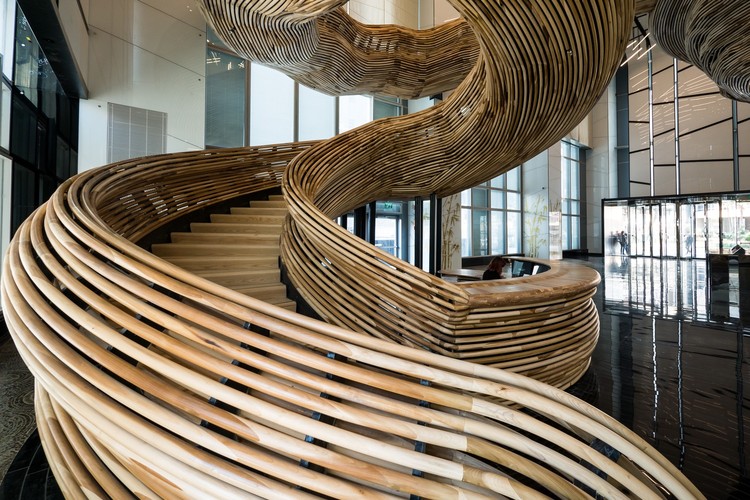
Just as a tree sways in a strong wind, wood has its own elasticity, and can be flexed to a certain extent before returning partially or completely to its original state when the force ceases. This elasticity depends directly on the type of wood and the dimensions of the piece to be curved. While sculpting wood to achieve the desired curves will always be an option, this method generates large amounts of waste and requires a very experienced workforce. Boat and furniture builders have been using curved wood for many years to adapt to hydrodynamic and ergonomic requirements. In buildings, however, these techniques are not so common. While sculpting the wood to reach the desired shape is always an option, this method generates a lot of waste and requires an experienced workforce. Other solutions create the illusion of organic volumes using straight components, which often achieves interesting results. Yet with the increasingly widespread use of wood as a primary building material, some architects have been looking to create directly organic forms for wooden structures, with several examples already having been made from Glued Laminated Wood. As architects, it is important to understand the process of creating these pieces to better design around them. The main methods for bending wood are:
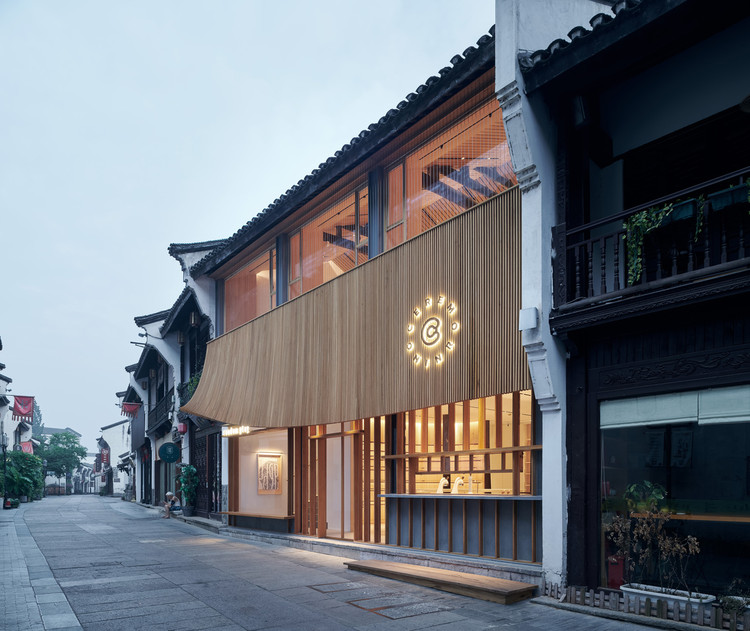
Steam Bending
German carpenter Michael Thonet pioneered one of the first methods of bending wood on an industrial scale, and his chairs, which are made with organic shapes, remain extremely popular today. In this mode of production, the wood fibers are not cut, which maintains the integrity of the piece. Rather, the method consists of heating the wood so that it becomes more malleable. A structure, called a steambox, is usually built to immerse the wood in an environment with high temperature, steam, and humidity. When it reaches 99 ° C, the lignin (a complex organic polymer that unites cellulosic fibers and gives rigidity to the plant cell wall) loses resistance, allowing the wood to be curved without significant resistance. After it is removed from the “oven,” the piece must immediately be taken to a mold and secured with staples. When the wood cools and dries, the piece will remain in the shape of the template.
Glued Laminated Wood
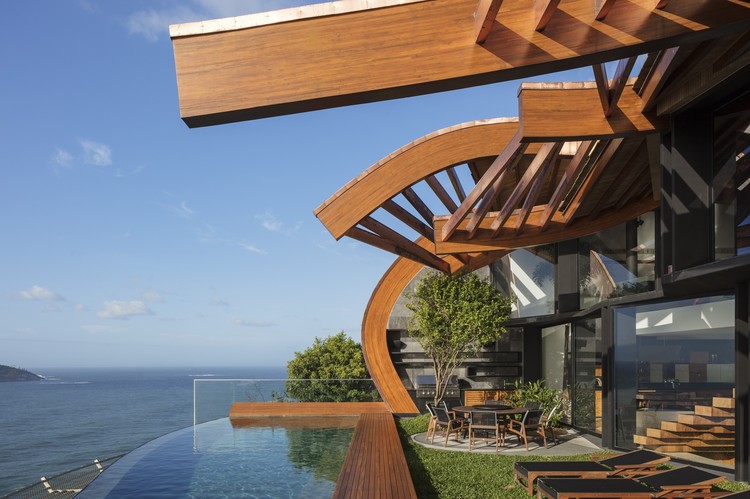
For architecture and larger pieces of wood, using Glued Laminated Wood is the most common method. However, it is also widely used for pieces of furniture or even for the manufacture of skateboards, as an example. Glued Laminated Wood, or Glulam, is a structural material manufactured by joining individual segments of wood glued with industrial adhesives (usually melamine or polyurethane resin adhesives). The resulting parts offer high durability and resistance to moisture, and can span large gaps and form unique shapes. This method does not involve heat or steam. If the pieces are glued following a mold with the desired curvature (while taking into account the restrictions of the material and the type of wood used), the end result will be a curved piece.
Kerf Cut
The Kerf cut method, in turn, is most often used for the manufacture of simple joinery. It is also possibly the simplest way to bend a piece of wood, without requiring machinery or large molds. However, it should never be considered for structural parts. This limitation occurs because the Kerf cut structurally weakens the wood, making spaced cuts on one side to allow the piece to curve. By applying force, it is possible to bend the piece, which will then generally be covered by a wooden sheet.
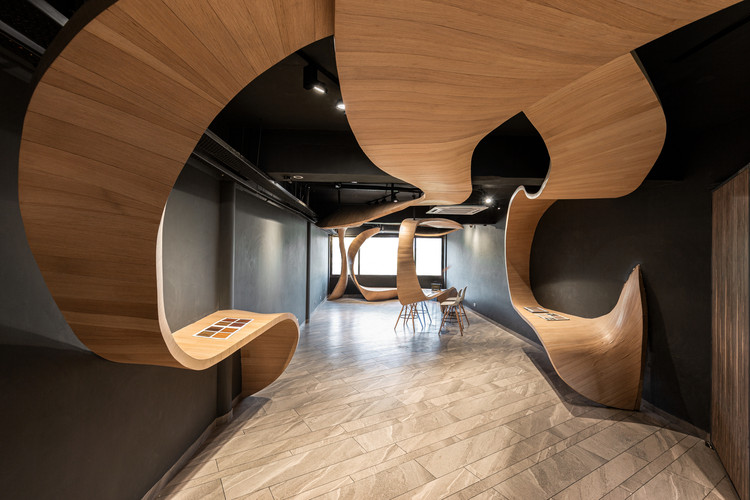
In addition to these more traditional methods, there have also been some innovations in wood bending techniques. When wood dries, it can twist and curve naturally due to the influence of the wood fibers inside the cut piece. Researchers from ETH Zurich, Empa and the University of Stuttgart took advantage of this characteristic - usually undesirable - to develop a new technique involving a controlled drying process that makes the wood panels bend in a predefined form without using force mechanics.
This self-modeling process is based in the natural swelling and contraction of the wood caused by the moisture content of the material. When the damp wood dries, it contracts more strongly perpendicularly to the fiber than along it. The researchers took advantage of this property by gluing two layers of wood together so that their grain directions opposed each other. This two-layer panel formed the basis of the new method. A wood component produced in this way remains dimensionally stable, even at floating humidity. The video below explains this method in more detail:
With the encouraged and more widespread use of wood as a building material, increased research and experimentation have also emerged. Masters like Zumthor and Alvar Aalto are known for pushing the possibilities of wood as a building material to the maximum. But understanding the restrictions and possibilities of the materials we work with is a starting point for any type of innovation. The possibilities of using wood and organic forms are numerous and when designing, it is essential to understand the complexities and seek new solutions.
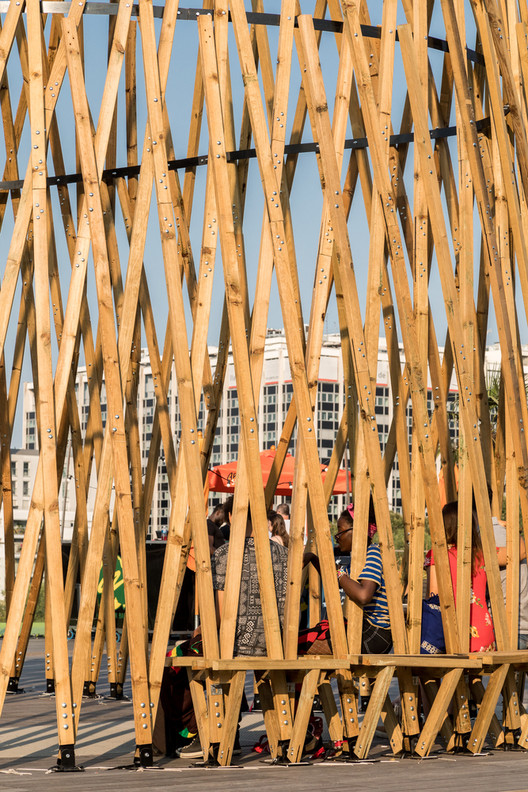
"wood" - Google News
August 03, 2020 at 06:35PM
https://ift.tt/2DsrYBV
How to Bend Wood - ArchDaily
"wood" - Google News
https://ift.tt/3du6D7I
No comments:
Post a Comment